Machines are the backbone of any manufacturing or food processing factory. This is because factories handle bulk raw materials, chemicals, packaging materials, and finished products. Although machines make work easier, they are prone to mechanical issues and could also expose workers to safety hazards.
Factories have to meet the standard safety requirements and follow standard practices to operate. However, the business owners should do much more to protect their workers and ensure high machine uptime.
Factory managers can use different approaches to improve safety, from guarding the machines to risk assessment, using safety equipment, and following best practices. This article will highlight effective tips and practices to enhance machine uptime and improve safety in the factories.
Machine Guarding
This is one of the best methods of reducing contact between people and machines. It involves installing a physical barrier or custom protective systems to shield employees from the safety hazards associated with moving parts of the machine.
Safety hazards in a factory with machinery include rotating parts that could cut the limbs, sparks that could cause fire, and flying debris that could injure workers. The protective system from the leading designers can help separate the machine operator and these hazards.
So, business owners should consider Enhancing Machine Uptime with Protective Systems. Besides preventing accidents and injuries, the protective systems guarding the machine ensure compliance with safety regulations.
Occupational Safety and Health Administration highlights the safety standards that factories should implement to protect workers. Machine guarding helps reduce the risk to the workers and minimize lawsuits and penalties associated with safety hazards.
Guarding machines with protective systems creates a comfortable and efficient workplace, where workers do not worry too much about their safety but instead focus on work. Besides, the physical barriers reduce the risk of accidents, injuries, and medical costs.
Accidents also cause machine downtime, which leads to losses. Therefore, machine guarding helps prevent downtime and save money that would cater to restoration costs, medical expenses, compensation claims, and compliance issues after an accident.
With the guards in place, machine operators feel motivated when working in a safe environment away from hazards such as flying debris. Confident and motivated workers usually commit to their work and are unlikely to switch jobs unexpectedly, which creates a harmonious and safer workplace.
Proactive Machine Maintenance
Machines rarely breakdown without warning signs such as strange noises, sparks, inefficiency, and high energy consumption. Therefore, machine operators will likely pick a few warning signs before the machine breaks down.
Unfortunately, some factory managers do not involve machine operators during maintenance. They believe that the mechanics can test, diagnose, identify worn out parts, replace them, test the machine and restore all parts. However, engaging machine operators and mechanics can help reduce the risk of accidents and enhance machine uptime.
The discussion between the machine operators and repair technicians helps highlight the safety concerns and what could be done to reduce the risk. Since operators use the machinery daily, they easily identify potential hazards and recommend safety measures that the mechanical engineers can implement.
After installing safety systems such as the physical barriers, the machine operators can provide invaluable input during regular risk assessment and provide insight on future changes. The machine operators report safety concerns such as close calls, accidents, near misses, mechanical problems to the mechanical engineer.
This firsthand information helps the machine experts and maintenance teams to develop practical solutions to safety concerns. For instance, the mechanical engineers can improve the running speed, the start and shut down mechanism, the operation procedures, or the position of the machine operator.
Engineers can also implement safety interlocks to reduce the risk of accidents. These interlocks stop the machine from operating if some safety conditions are not met. For instance, the machine can stop if the guards are not in place or if a worker enters a restricted area.
The machine operators can learn a few things from the repair technicians or mechanical engineers. They learn the potential risks of using the machine, warning signs to observe, how to stop the machine during emergency, and how to clear machine jam. They also learn basic maintenance and inspection tips to avoid operating a faulty machine likely to breakdown or cause injuries.
Proper documentation is key for ensuring workplace safety and compliance with industry regulations. Understanding who is responsible for providing SDS in the company helps operators access crucial safety data sheets, which outline handling procedures, potential hazards, and emergency response measures for various materials. Having this information readily available allows machine operators to work more safely and efficiently while reducing the risk of accidents. When combined with hands-on training, proper documentation creates a well-rounded approach to workplace safety and equipment management.
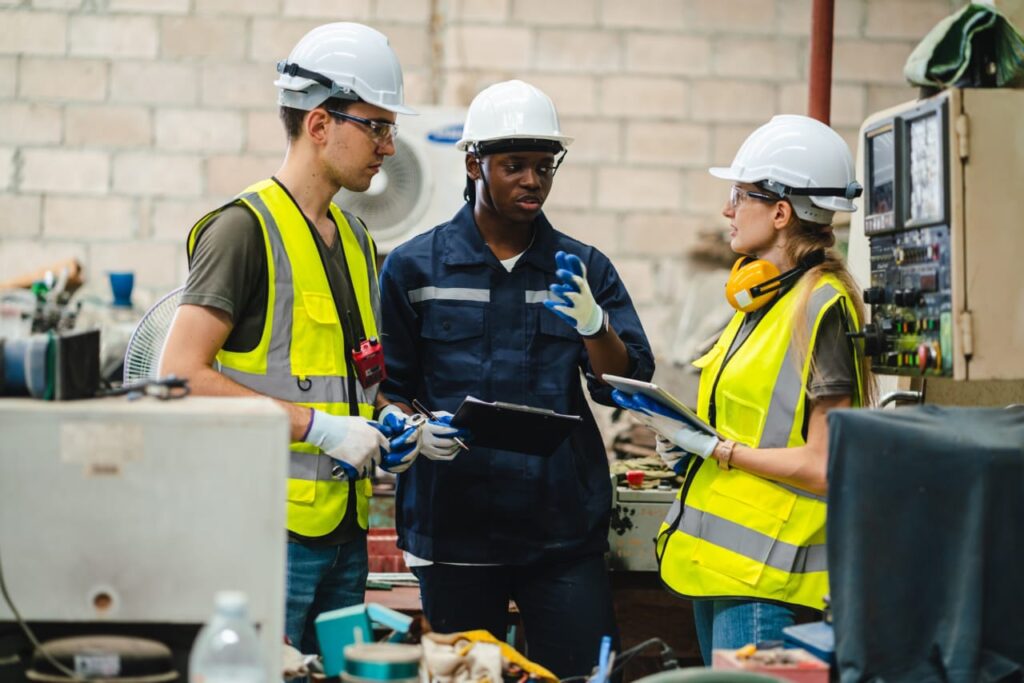
Train Operators and Other Employees About Machine Safety
Factory owners can reduce the chances of accidents and machine failure by training employees about the machines in the work place. This is because some machines breakdown or cause injuries because the operators or other workers do not follow safety and maintenance procedures.
Employees might seem competent and experienced but might lack basic skills for inspecting and solving minor mechanical issues affecting the machine. Therefore, organizing employee training will help staff use the machine for the right type of work, apply safety features, prevent injuries, and optimize productivity.
After the training, the employees can work efficiently with minimal risk of injuries. They also embrace a culture of safety in the workplace since they will quickly identify and report hazards for timely intervention. Reduced cases of injuries and accidents reduces potential compensation lawsuits and downtime when machine and employees do not work.
Use Protective Gear and Adhere to Standard Operating Procedures
Machines work with raw materials and chemicals that can cause harm to human. However, employees can use protective equipment to reduce the risk of injuries despite operating hazardous machines. They can use gloves, goggles, safety boots, reflector jackets, earplugs, facemasks, and safety jackets.
The employees must also follow standard operating procedures for inspecting and operating the machine. For instance, each operator should have a safety checklist to ensure certain safety standards are met before running the machine.
The standard operating procedure should be correct, clear, concise, accessible, and effective. If the machine is improved or replaced, the standard operating procedure and checklists should be updated to reflect the latest features and procedures.
Factory business owners and workers can implement safety features and follow relevant procedures to improving machine uptime. These safety measures and ideas can also help reduce the risk of accident and keep machines running with minimal downtime. However, some safety measures require a seasoned professional to optimize safety without compromising productivity. Therefore, factory owners should hire experts to implement these safety measures and improve machine uptime.