Metalworking is a time-honored craft steeped in both art and technical precision, merging creativity with scientific principles. From ancient blacksmiths to modern industrial processes, metalworking has evolved significantly, shaping civilizations and livelihoods. Today, it encompasses a wide range of techniques and practices, making it essential for various industries, including automotive, aerospace, and construction. Understanding the foundational elements of metalworking can provide insights into its applications, methods, and the skills required to excel in this field.
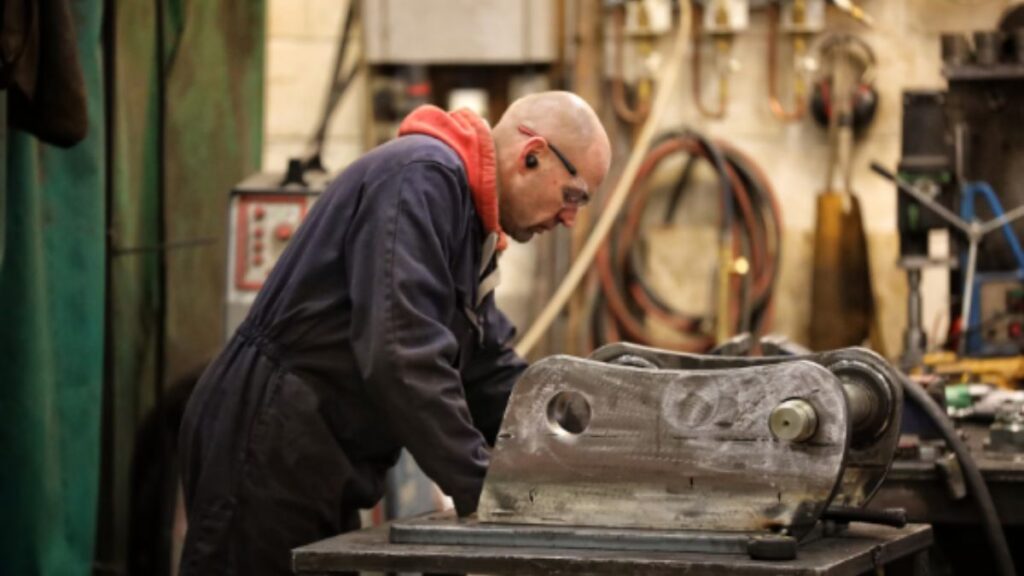
The Evolution of Metalworking Techniques
It has undergone significant transformations, from primitive methods to sophisticated technology. Initially, metal was hammered into shape by hand, with artisans using basic tools to create everyday items. Over centuries, techniques like casting, forging, and welding emerged, allowing for more complex and durable creations. The Industrial Revolution marked a pivotal moment, introducing machinery and automation that enhanced productivity and precision. This evolution continues today, with advancements in robotics and computer-aided design, further pushing the boundaries of what is possible in metalworking. Understanding these changes is crucial for anyone looking to explore this dynamic field.
Key Metalworking Processes
At the heart of metalworking lies a variety of processes, each with its specific applications and advantages. These include:
- Casting: A process where molten metal is poured into a mold to solidify. It allows for intricate shapes and is commonly used in industries from jewelry to engine manufacturing.
- Forging: This involves shaping metal through compressive force. The result is typically stronger than other methods, making it favored for components exposed to high stress.
- Machining: A subtractive process where material is removed from a metal piece to achieve desired shapes and finishes. This precision is vital in manufacturing parts that fit together seamlessly.
- Welding: Joining metals through heat, welding is essential for constructing everything from buildings to complex machinery. Understanding different welding techniques broadens the skillset of any metalworker.
Each of these processes has its unique requirements and challenges, making proficiency in several techniques beneficial for those in the metalworking domain.
Essential Tools and Equipment for Metalworking
To effectively engage in metalworking, practitioners must equip themselves with the right tools and machinery. Depending on the technique being employed, various tools may be necessary. For example, a forge is essential for blacksmithing, while lathes and milling machines are fundamental for machining tasks. Safety equipment such as gloves, goggles, and appropriate clothing cannot be overlooked due to the inherent risks involved in working with heavy machinery and molten metals. Proper training in tool usage helps ensure safety and enhances efficiency. Companies that specialize in supplying tools, including Elyria Spring and Stamping, as well as some similar ones, provide invaluable resources for both amateurs and professionals in the metalworking field. Access to high-quality tools can significantly influence the quality of the finished product and the overall success of metalworking projects.
Metallurgy: The Science Behind Metalworking
Understanding metallurgy—the study of metals, their properties, and behaviors—is crucial for effective metalworking. Knowledge of different metal types, including ferrous and non-ferrous materials, informs decisions on which material to use based on application requirements. For instance, steel is highly versatile due to its strength and durability, making it suitable for construction. In contrast, aluminum is favored for its lightweight properties and resistance to corrosion, ideal for aerospace applications. Metallurgy encompasses the effects of heat treatment on metal, influencing hardness, ductility, and tensile strength. This depth of understanding allows metalworkers to tailor their methods to achieve the desired characteristics in their final products.
Applications and Industries Utilizing Metalworking
The versatility of metalworking makes it an integral part of numerous industries. In the automotive sector, for instance, metal is engineered for the manufacturing of everything from engine components to structural elements. Aerospace relies on precision-engineered metals to ensure safety and performance in flight. Construction utilizes metalworking for a vast array of applications, including frameworks, fittings, and decorative elements. The burgeoning field of renewable energy, especially involving solar and wind technologies, showcases how metalworking adapts to meet contemporary needs. As industries continue to evolve, the demand for skilled metalworkers is likely to rise, emphasizing the importance of honing these skills.
Learning Metalworking: Skills and Education
For those interested in pursuing metalworking, various pathways exist for acquiring skills. Vocational schools, community colleges, and apprenticeships provide hands-on training essential for mastering metalworking techniques. Courses often cover safety protocols, tool operation, and specific processes like welding and machining. A blend of traditional craftsmanship and modern technology is increasingly emphasized, equipping students with relevant skills for the job market. Continued education through workshops and online resources can also enhance expertise. The journey of learning metalworking can lead to fulfilling careers, artistic expression, and the creation of tangible works that embody both skill and innovation.
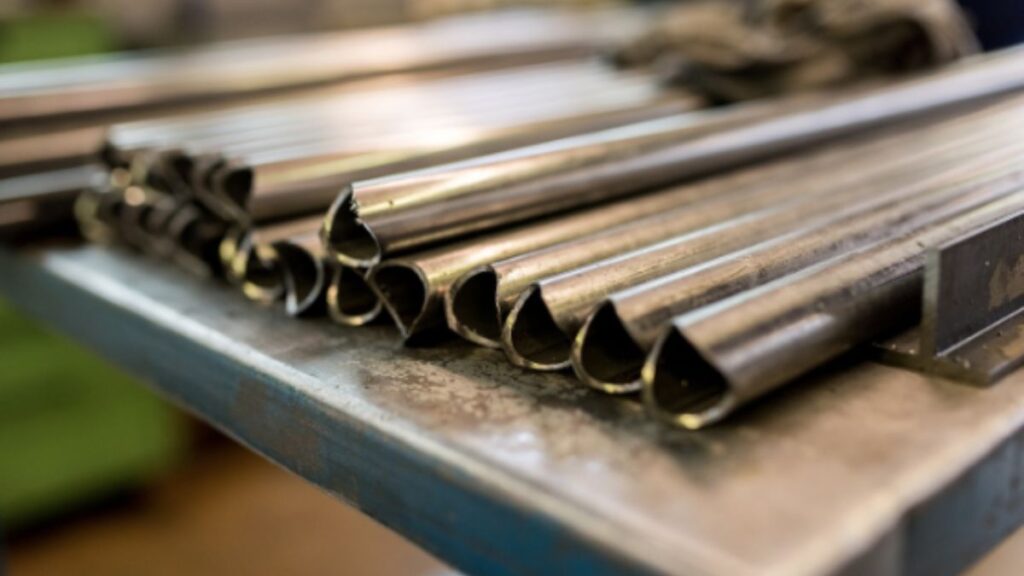
Through a blend of history, techniques, tools, and applications, metalworking stands out as a multifaceted discipline that appeals to both creators and engineers. As it continues to evolve with technology and societal needs, it invites a new generation to explore its depths and appreciate the beauty and intricacy of metalworking.