Ensuring safety and quality in industrial settings is paramount, and non-intrusive inspection (NII) technologies are leading the charge in redefining these safety standards. Various industries—ranging from oil and gas to manufacturing—are increasingly deploying these advanced techniques to maintain and enhance their operational integrity. By eliminating the need for physical alterations or disruptions, these technologies allow for deeper insights into structural and mechanical elements without compromising safety or productivity.
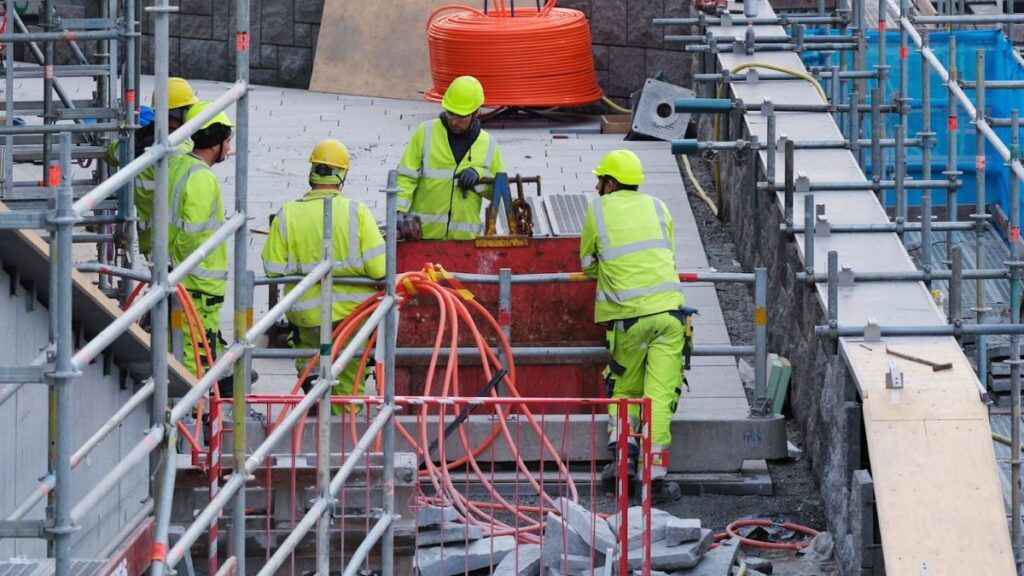
The Rise of Non-Intrusive Inspection Technologies
In recent years, the adoption of NII technologies has surged, driven by the need for more accurate, efficient, and cost-effective inspection methods. Traditional inspection techniques often require downtime or destructive methods that can incur substantial costs to companies. According to a report by the International Society for Optics and Photonics, NII technologies can reduce costs associated with inspection by up to 30% while improving the reliability of the assessment. This shift promises not only to enhance operational efficiency but also to support compliance with stringent safety regulations. Advancements in areas such as ultrasonic testing, radiography, and thermography have paved the way for this evolution. These technologies leverage modern science to penetrate materials and detect flaws without having to disturb the component or structure being analyzed.
Industry Applications of Non-Intrusive Inspection
Non-intrusive inspection technologies are versatile, finding applications in various sectors. The oil and gas industry benefits significantly, from utilizing NII for pipeline integrity management, which is critical for preventing leaks and ensuring environmental safety. Using advanced NII can improve detection rates of pipeline anomalies, thereby preventing disasters before they occur. Similarly, manufacturing plants employ NII technologies during routine maintenance checks to monitor machinery and infrastructure. By continuously assessing equipment without shutting down operations, businesses can maintain high productivity levels while ensuring that safety standards are upheld. Streamlining these processes has resulted in companies reporting a 25% increase in overall efficiency, as downtime is substantially minimized.
Key Benefits of Non-Intrusive Inspection
Embracing NII technologies offers numerous benefits that extend beyond immediate cost savings. One significant advantage is the enhancement of operational safety. As NII techniques allow for real-time monitoring, they provide early warnings of potential failures or hazards. This proactive approach to safety reduces the risk of accidents and leads to safer work environments. NII methods are environmentally friendly. Traditional inspection methods can lead to contaminants leaking into the environment during intrusive procedures. As regulations tighten regarding environmental impact, adopting industry-leading non-intrusive inspections helps organizations remain compliant while showcasing their commitment to sustainability. Conversely, NII technologies mitigate such risks by minimizing waste generation and limiting exposure to toxic substances.
Challenges and Considerations
While the rise of non-intrusive inspection technologies comes with many benefits, there are challenges that industries must navigate. One of the primary concerns is the initial investment required for advanced NII equipment and training personnel. Companies must weigh the long-term savings and efficiency gains against upfront costs to determine the viability of adopting these technologies. There is a learning curve associated with implementing new technologies. Organizations must invest in comprehensive training programs to ensure their workforce can effectively utilize and interpret the results produced by NII equipment. Failure to do so could undermine the advantages that these systems provide.
Future of Non-Intrusive Inspection Technologies
The future of non-intrusive inspection technologies looks promising, consolidating its position as an integral part of safety management protocols. With rapid advancements in artificial intelligence and machine learning, there are opportunities to enhance the accuracy and efficiency of inspections further. Future NII systems can potentially utilize these technologies to analyze data trends, predict equipment failures, and suggest timely maintenance interventions. As more sectors recognize the benefits of NII, we can expect greater collaboration among industries looking to innovate and improve safety standards. This shared approach could lead to standardized practices that elevate safety across the board, allowing companies to operate more effectively while ensuring the well-being of their workers.
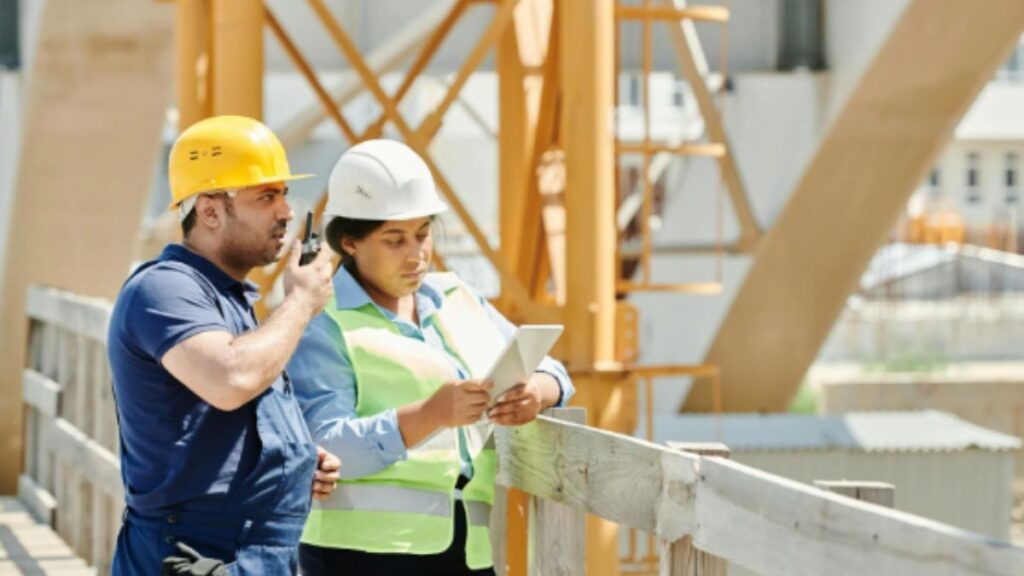
Non-intrusive inspection technologies are undeniably transforming safety standards across various industries. Their ability to provide accurate assessments without disrupting operations translates into remarkable cost savings and improved safety outcomes. As these technologies continue to evolve, they promise even greater insights and efficiencies for organizations committed to maintaining high safety standards. Embracing non-intrusive inspection not only strengthens compliance with regulations but also fosters a culture of innovation that prioritizes safety and sustainability.