Choosing the right industrial scale is crucial for ensuring accuracy, efficiency, and compliance in your operations. Whether you need a scale for manufacturing, shipping, or laboratory purposes, the decision can impact productivity and the bottom line. Understanding the key factors that influence your choice will help you make an informed decision that suits your specific needs.
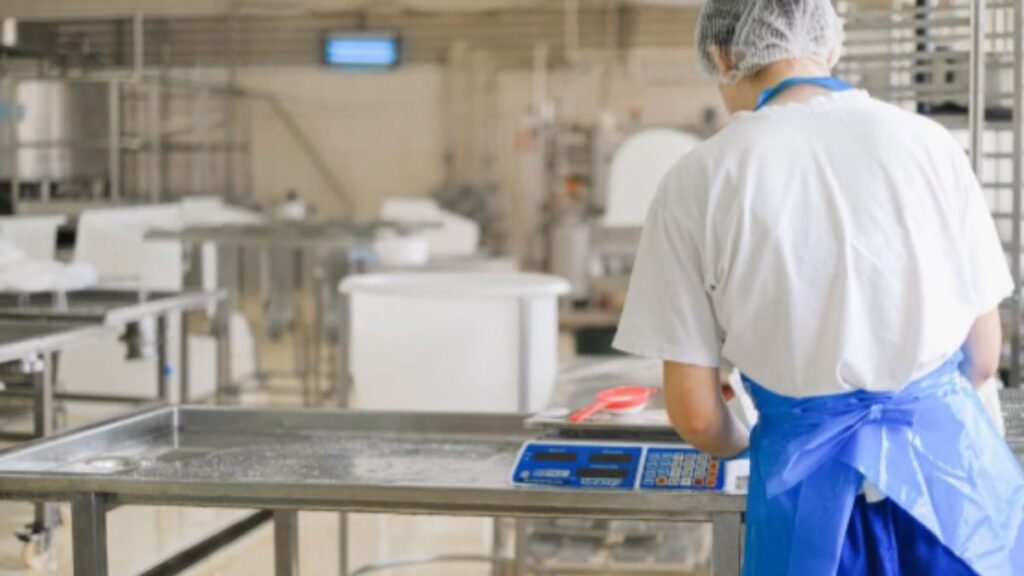
Consider Weight Capacity and Range
Overloading a scale can cause inaccuracies, potential damage, and even safety risks. Determine the maximum weight you expect to measure and make sure the scale’s capacity can handle it. Consider 188Scales for a reliable, high-performance industrial weighing solution tailored to meet your specific needs and ensure optimal accuracy and durability. If you expect a wide range of weights, choose a scale that can handle both low and high capacities without compromising accuracy.
Understand the Type of Scale You Need
Before diving into the details, determine the type of industrial scale required for your operations. Different industries and processes need specific types, such as platform scales, bench scales, or floor scales. Platform scales are ideal for weighing large items or pallets, while bench scales work best for small to medium-sized items. Assess the size and weight capacity of the items you plan to weigh to ensure you choose a scale that meets your operational requirements.
Accuracy and Precision Matter
When selecting a scale, pay attention to its accuracy and precision. An accurate scale ensures that every measurement is correct, which is critical in industries such as manufacturing, food production, and pharmaceuticals. Even minor discrepancies can lead to waste, loss of resources, or compliance issues. Choose a scale that offers the level of accuracy needed for your operations and ensures precision within your specific weight range.
Quality of Calibration
The calibration of your scale plays a crucial role in ensuring accurate readings. Regular calibration is necessary to maintain the scale’s precision over time, especially in environments where scales are frequently used or subjected to rough handling. Without proper calibration, a scale’s accuracy can degrade, leading to errors in measurements and potentially costly mistakes, such as over- or under-ordering materials.
Resolution and Readability
Consider the scale’s resolution, which refers to the smallest increment it can measure. A scale with high resolution provides more precise readings, which is important when dealing with small quantities or when extreme accuracy is required. Whether you’re weighing ingredients in a production process or measuring small components, having a scale that delivers fine resolutions can significantly impact the quality of your output.
Repeatability of Measurements
A good industrial scale should provide consistent measurements each time an item is weighed. Repeatability refers to the scale’s ability to produce the same results under the same conditions. This is especially important in environments where multiple measurements of the same item are required. Scales with low repeatability can cause variability in the results, leading to operational inefficiencies and increased risk of errors.
Tolerance and Error Margins
Every scale comes with a specified tolerance level, which defines the acceptable range of error. The tolerance level should match the precision requirements of your operation. For example, industries like pharmaceuticals or aerospace often require scales with very low tolerance levels, as even slight deviations could have serious consequences. Be sure to select a scale that meets the necessary tolerance standards for your particular application.
Durability and Material Quality
Industrial scales need to withstand tough working conditions. Look for scales made from high-quality materials like stainless steel, which is resistant to corrosion, wear, and tear. If you operate in an environment with harsh conditions like extreme temperatures or exposure to moisture, choose scales designed for those conditions. Ensure the scale you choose is built to last and can endure the environment where it will be used.
Integration with Other Systems
Consider how well the scale integrates with your existing systems, such as inventory management, shipping software, or manufacturing equipment. Scales with built-in connectivity, like Bluetooth or Wi-Fi, can help streamline operations by transmitting data directly to your system, reducing the chance for errors and speeding up processes. If you already use software to track weights or shipments, ensure your scale can easily connect to those systems.
Ease of Use and Maintenance
The scale you choose should be easy to operate and maintain. A user-friendly interface with clear displays and simple controls will save time during daily operations. Also, consider the maintenance requirements of the scale. Choose a model that is easy to clean and calibrate. Regular maintenance ensures your scale remains in good working order and continues to provide accurate readings.
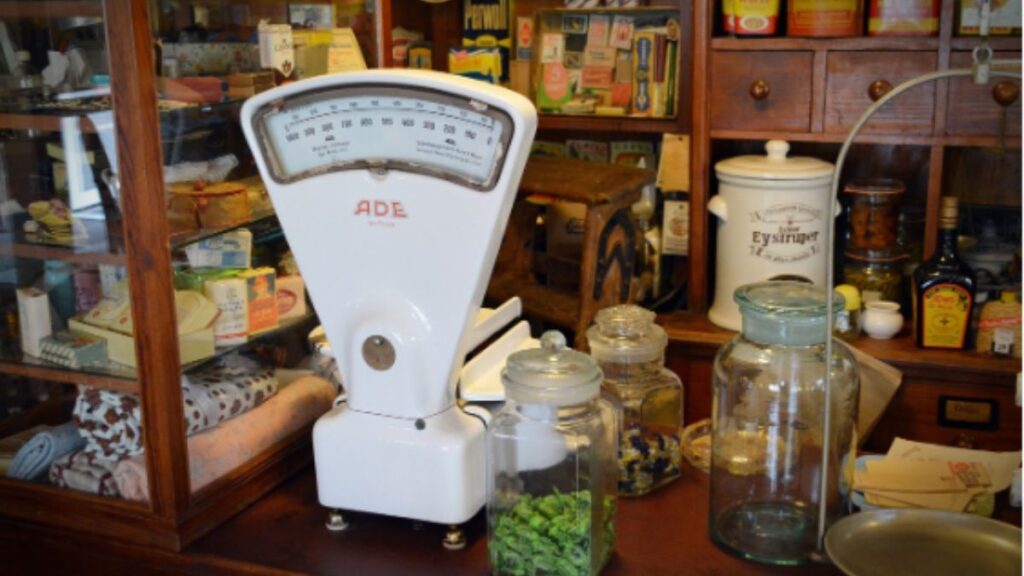
Choosing the right industrial scale is more than just a purchase – it’s an investment in the efficiency and accuracy of your operations. By considering the type, weight capacity, accuracy, durability, integration capabilities, and ease of use, you can select the scale that best fits your needs. Take the time to evaluate your options carefully, and ensure the scale you choose will support the growth and success of your business.