Chemical mixing is a fundamental process in all kinds of industries, including pharmaceuticals, food production, petrochemicals, and materials science. Effective mixing provides homogeneity, enhances the reliability of chemical reactions, and produces the highest quality product. Read below for an exploration of the principles of chemical mixing, the techniques employed, and the broad applications of the chemical mixing process across different sectors.
Principles of Chemical Mixing
The primary objective of chemical mixing is to achieve a uniform distribution of components, certifying consistency in composition and properties. These are the top principles that govern mixing:
Diffusion: The natural movement of molecules from high to low concentration, leading to homogeneity over time.
Convection: The bulk movement of fluids, which speeds up the mixing process and allows for large batches to be made at once.
Shear Forces: The application of mechanical forces that create gradients in velocity, promoting dispersion and dissolution.
Turbulence: The chaotic flow of fluids that increases contact between different chemical species, leading to faster and more effective mixing.
Techniques of Chemical Mixing
Chemical mixing techniques vary depending on the nature of the materials being mixed (liquids, gases, solids, or multiphase systems) and the desired outcome. If your business works with these kinds of materials and you need reliable software and machinery, take a look at visimix.com for all of the best options. When it comes to mixing chemicals, it all comes down to the following common techniques:
Batch Mixing: This is a controlled process where ingredients are mixed in a single vessel for a defined time before being deposited elsewhere or split into smaller units. This technique is most common in the pharmaceutical and food industries.
Continuous Mixing: Components are continuously fed and mixed in a steady-state process with this technique. This is widely used in large-scale chemical production.
Static Mixing: This technique uses fixed elements inside a pipeline to mix fluids without moving parts, reducing energy consumption and maintenance.
Agitation: With the use of mechanical stirrers, paddles, or impellers to create fluid motion, materials are mixed. This is common in bioreactors and chemical reactors.
Ultrasonic Mixing: High-frequency sound waves are used for this technique to break apart particles and enhance dispersion. This is especially useful in nanoparticle synthesis and emulsification.
Emulsification: This is the process of mixing immiscible liquids like oil and water. It is done by using surfactants and high-shear mixers to create stable emulsions. When a liquid is added to a surfactant, the surface tension is reduced, increasing its spreading and wetting properties. This is useful in the textile industry for dying fabrics.
Applications of Chemical Mixing
Pharmaceutical Industry: Produces uniform drug formulation, enhances bioavailability, and maintains the stability of medicinal compounds.
Food and Beverage Industry: Used in blending ingredients, creating emulsions, and providing consistency in taste and texture.
Petrochemical Industry: Facilitates the mixing of crude oil fractions, refining processes, and production of fuels and lubricants.
Cosmetics and Personal Care: Essential for formulating lotions, creams, and perfumes to make sure they have a smooth texture and long shelf life.
Paints and Coatings: Achieves uniform color distribution, viscosity control, and optimal drying properties.
Water Treatment: Used in chemical dosing, coagulation, and flocculation to purify water and remove contaminants.
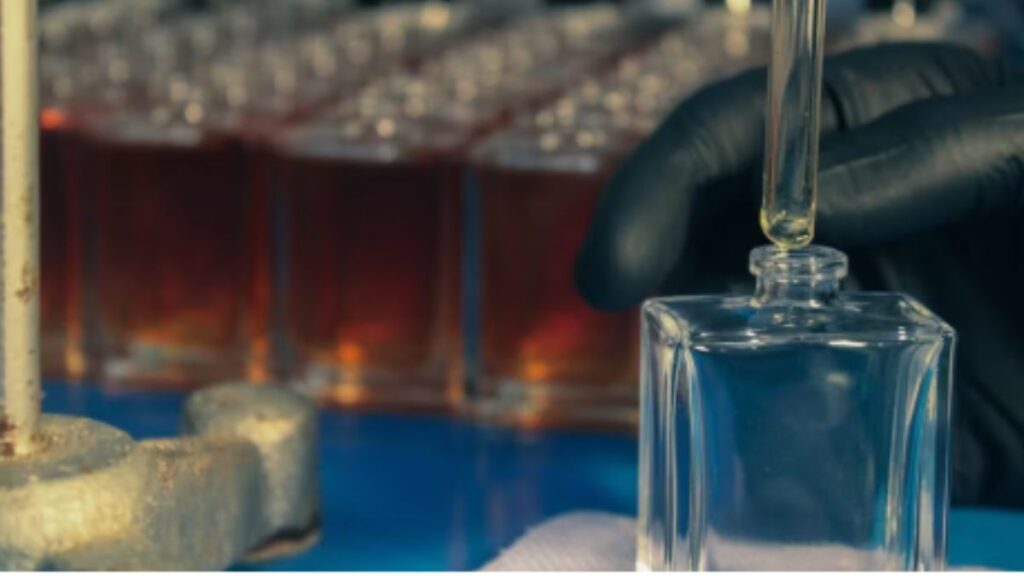
Chemical mixing influences product quality, safety, and efficiency in industries around the world. Understanding the principles, employing the right techniques, and optimizing mixing processes can lead to improved outcomes in manufacturing and research. With advancements in technology, new mixing methods continue to emerge, further enhancing the precision and effectiveness of chemical processing.