As the demand for customized and low-volume products grows, manufacturers often grapple with the best methods to meet these challenges. Among the various techniques available, injection molding stands out as a preferred option for many. This manufacturing process provides flexibility, efficiency, and the ability to produce intricate designs, making it incredibly valuable for small-scale needs. Understanding the strengths of this technique can guide businesses in making informed decisions, ensuring quality output and reduced costs.
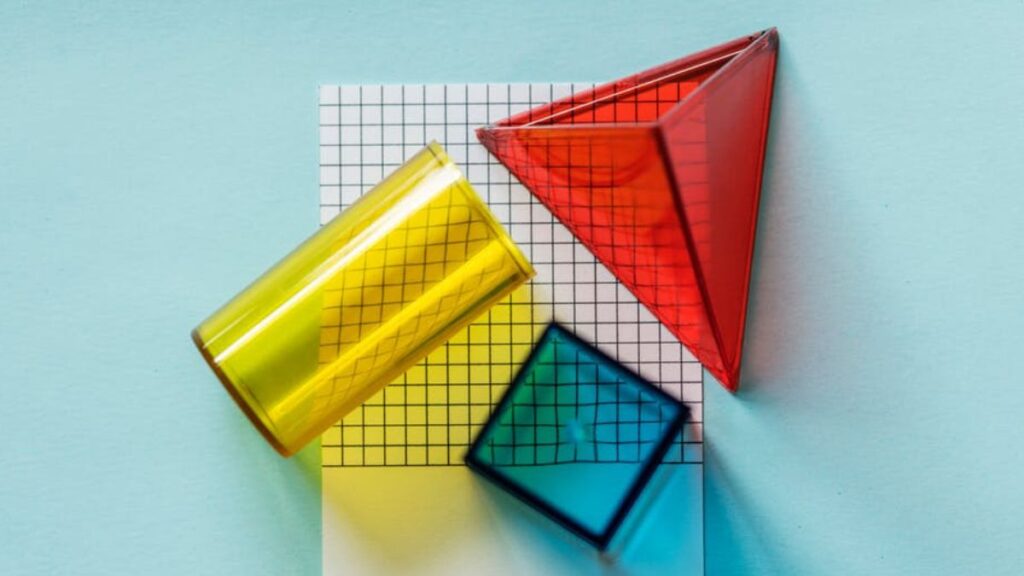
Understanding Injection Molding
Injection molding is a manufacturing process that involves injecting molten material into a pre-designed mold cavity. Upon cooling, the material solidifies to form a specific shape. Highly versatile, this technique can work with a range of materials, including thermoplastics, thermosetting plastics, and metals, applicable across varied industries. The ability to create complex geometries is one of the principal benefits, as the intricate mold designs allow for precision engineering. Injection molding supports mass production, paving the way for efficient manufacturing runs that can deliver high-quality parts consistently.
While larger-scale production may be the initial thought with this method, it is equally effective for small-scale productions. To learn more about small-part injection molding and implement the right solution, you can go here to consult the experts. You will be sure to order molds suited to your specifications without overcommitting resources.
Benefits of Injection Molding for Small-Scale Production
For small-scale manufacturers, injection molding brings numerous benefits. First, the production speed is significant; once the mold is made, the cycle time for producing each piece is negligible. This rapid turnaround is a necessity for businesses needing to deliver products to market quickly. The initial investment, often a concern for small manufacturers, proves beneficial in the long run. The costs associated with the design and creation of molds can be recuperated through the efficiency and reduced waste produced during the operation.
The consistency in quality of every piece reassures manufacturers of their output’s reliability. A major aspect of this method is the ability to undertake complex and multifunctional designs. Many small-scale manufacturers benefit from producing components that integrate multiple functions into one part, reducing assembly time and potential errors in production.
Customizability of Injection Molded Parts
Manufacturers can create molds that exactly meet their specifications so that every aspect of the final product adheres to their standards. This customization enables businesses to cater to niche markets and specific consumer preferences. In industries like automotive or consumer goods, where consumer preferences often dictate design, you want to tailor parts that resonate with customers.
Such customization is not limited to aesthetics; functional elements such as drawings, features, and hinges can all be personalized. An ongoing dialogue with clients around customizing molds and designs significantly aids in fostering business relationships.
Cost Efficiency in Production
Injection molding presents an opportunity to reduce production expenses. When the upfront costs of designing and producing the molds are absorbed, the average cost per part diminishes dramatically. This decreases waste and results in consistent quality output, translating into fewer defective items and less material wastage.
The efficient nature of the process means that less energy and resources are used compared to other manufacturing methods. The possibility of duplicating parts efficiently without significant additional costs proves advantageous for small businesses aiming to sustain themselves in a competitive market.
Challenges Faced in Injection Molding
Despite its numerous advantages, injection molding is not without challenges. One of the significant hurdles is the initial investment required. Crafting high-quality molds can be costly, particularly for small businesses trying to juggle their capital needs. This upfront capital might deter some manufacturers from adopting this process.
Another challenge can arise from the materials used: the selection of the appropriate material that meets both functional requirements and cost-effectiveness is a must. Businesses must be well-informed regarding material compatibility with the molding process to ensure the desired properties are attained. Any nuances overlooked at this stage can result in larger issues later in the production cycle.
Impact of Technology on Injection Molding
Advancements in software for design and simulation streamline the mold-making process, ensuring higher accuracy and reducing the trial-and-error stages that have traditionally burdened manufacturers. The integration of 3D printing technologies into the mold-making process allows for rapid prototyping, which accelerates the time from concept to completed product.
Innovations in materials have expanded the range of possibilities for manufacturers. From bioplastics to advanced composites, these materials provide novel properties that cater to the evolving demands of modern industries. Automation and robotics streamline the injection molding process, increasing production speeds while minimizing human error. Automated systems can monitor processes in real-time, allowing for prompt interventions to correct issues that arise.
The Future of Injection Molding in Small-Scale Manufacturing
As we move forward, the future of injection molding looks promising for small-scale manufacturers. The growing emphasis on sustainability ensures that processes adapt to incorporate eco-friendly practices and materials, propelling businesses towards greener production avenues.
Consumer expectations shift rapidly; small-scale manufacturers must be prepared to adapt to such changes without undergoing extensive retooling. The flexibility offered by injection molding, through customizable molds and rapid production capabilities, rightfully positions it as a key player in this evolution.
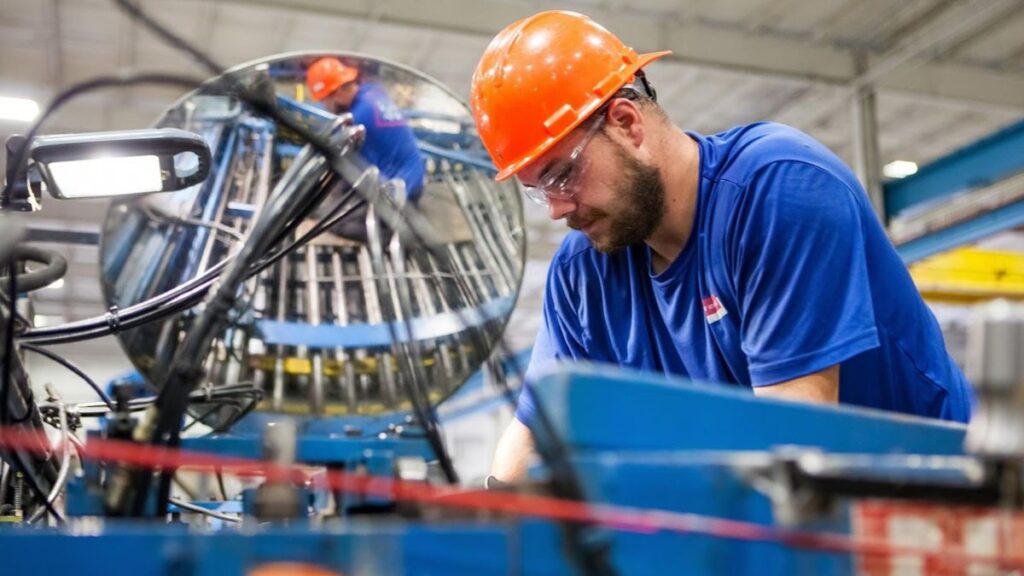
Businesses that embrace these changes, focusing on delivering quality products efficiently, will be well-prepared for the dynamic market landscape ahead. This method of production is set to define a new era of small manufacturing efficiency and innovation.